Structural fabrication stands as the foundation of marine engineering for the construction industry. Success in creating steel structures resistant to marine conditions takes remarkable effort when used for ship hulls and offshore oil rigs. The fabrication processes for marine engineering construction require strict alignment with project specifications to deliver structures that are structurally strong and durably built at sea.
Following industry standards in fabrication represents both a regulatory necessity and a proven method to achieve durability in structures subjected to corrosion and constant wave motion under saltwater exposure and mechanical stress conditions.
Key Standards in Structural Steel Fabrication for Marine Vessels
The fabrication of structural steel components for marine environments demands exact coordination among materials selection and production techniques, and technological platforms.
Steel beams, along with I-beams and steel plates, appear frequently in marine shipbuilding operations because of their impressive mechanical properties. Steel components need fabrication and corrosion-resistant treatment for precise project adherence.
Professional fabrication teams follow specific welding techniques, such as MIG welding and arc welding, to assemble and weld steel components. Every fabricator is trained to deliver high-quality joints that meet building codes and can endure marine forces. Many shipyards also prefabricate structural components in a controlled manufacturing facility to maintain consistency before transporting them to the construction site for final installation.
The Stages of Structural Steel Fabrication
The steel fabrication process is a complex one that goes through several stages, each of which contributes to the performance of a structure in extreme situations. The following paper works to outline the processes in the steel fabricating process, starting from the concept and right up to the end.
Design Specifications and Drawings
All marine projects start with exact drawing work, which achieves design specifications. Through their use of CAD systems, engineers design steel structures while taking into account both structural loading factors and expected environmental conditions. Building Information Modelling (BIM) gives stakeholders an opportunity to partner and see structural component integration through visual presentations.
Shop drawings play a crucial role in translating engineering plans into executable fabrication tasks. They include every measurement, material type, and tolerance required to fabricate according to the exact specification.
Material Preparation and Cutting Techniques
Steel fabrication specialists shape metal pieces after design completion by utilising contemporary cutting equipment. Modern methods of steel cutting, such as laser cutting tools, plasma torches, and water jets, ensure neat cutting with very little wastage of material. The range of steel sections that can be processed includes flat plates, together with curved tube bending elements, through these advanced cutting methods.
Workshops equipped with CNC (Computer Numerical Control) equipment operate machinery for making repeated, precise cuts rapidly. Machine technology ensures steel parts achieve precise measurements, which facilitates flawless fitting during final production.
Assembly and Welding Techniques
Next comes the assembly stage, where steel is joined together to create different frameworks. It may comprise rivets, bolts, or various types of welding processes, depending on the role of the structure to be constructed.
Common methods include MIG welding for clean, quick joints and arc welding for deeper penetration in heavy-duty fabricated structural steel. Skilled welders ensure the alignment and strength of each connection, working closely with riggers and crane operators to position components.
Some projects require machinery or cranes to lift large steel components into place safely. The entire process is overseen by experienced fabricators who understand the critical nature of marine construction.
Quality Control and Inspection
A thorough series of quality checks begins after structure assembly is complete. NDT, or non-destructive testing methods, made up of ultrasonic testing, radiography, and magnetic particle inspection, allow for internal flaw detection that avoids damage to materials.
Weld seam inspections and coating verifications, and dimensional tolerance assessments accompany NDT as part of the fabricator’s quality checks. The application of powder coating or anti-corrosive coatings serves to boost the structure’s corrosion resistance capabilities.
Through strict quality commitment across all inspection stages, manufacturers can achieve reliable product performance in corrosive, high-pressure operational conditions.
K-Marine: Your Trusted Ship Repair and Maintenance Provider in Singapore
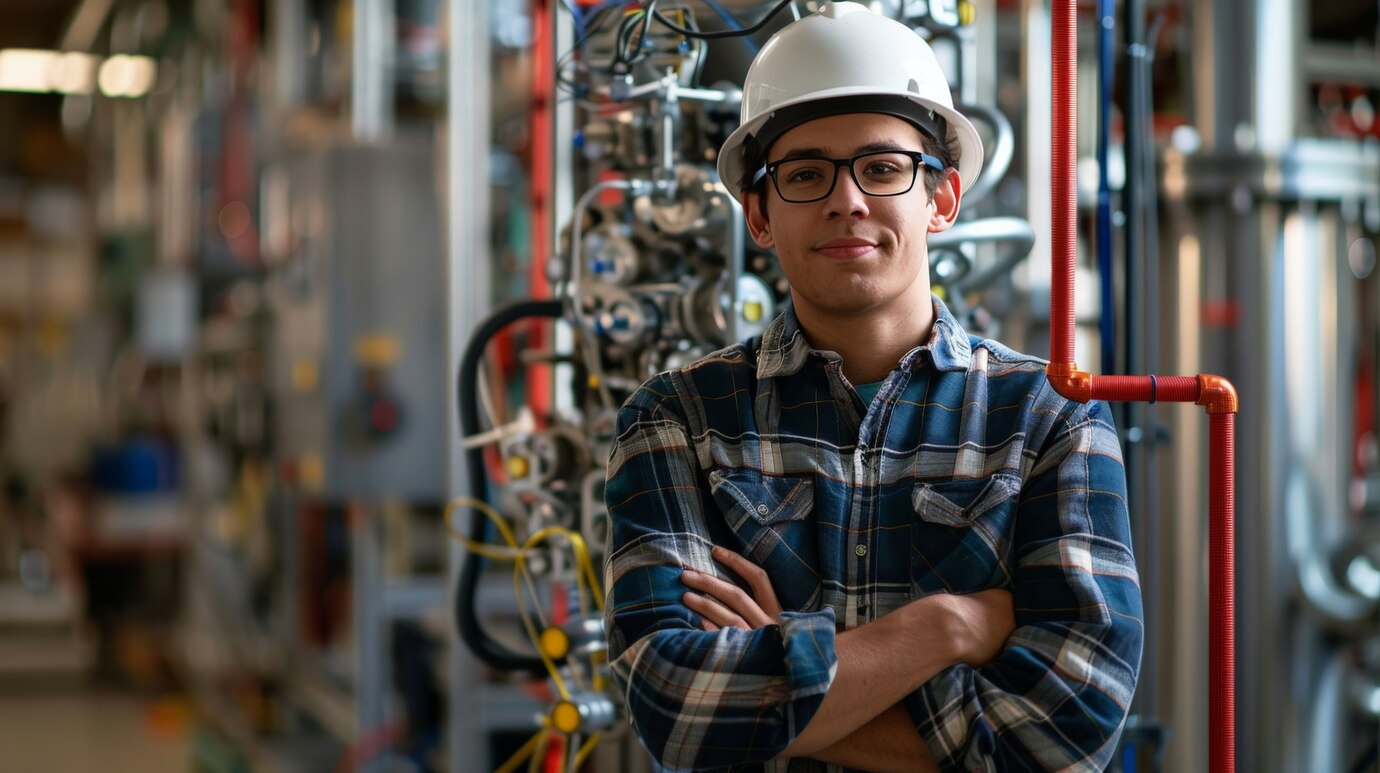
K-Marine understands that marine construction depends strongly on accurate fabrication techniques. Our leading ship repair and maintenance fabrication services operate from Singapore as an industry leader. Our team of experts combines a deep marine engineering background with extensive international know-how and leading-edge fabrication techniques.
Whether it’s working on steel frameworks, repairing damaged structural components, or custom-building modules in our industrial equipment workshop, we tailor every project to your unique project requirements.
Final Thoughts
Fabrication processes steel from its unprocessed state into structures that can handle maritime environments under harsh conditions. Exactly cut steel combined with expert welding techniques, along with total inspections, creates structures that maintain strength and durability throughout multiple decades of maritime service.
K-Marine provides dependable marine fabrication alongside efficient ship maintenance services in Singapore. The people at our company provide you with affordable, high-quality solutions that are customised specifically for your vessels. Call us today and let us help you maintain your vessel!